Metal and machining technology – an evolving field
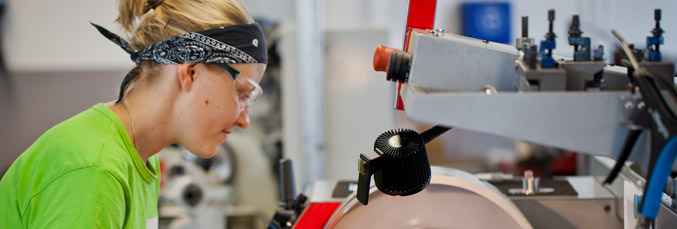
Technical comprehension and manual dexterity are fundamental requirements for those working in metal and machining technology. Today, however, rapid technological developments and evolving types of company organisation require even more: flexibility, the ability to work in a team and openness to new ideas to name just a few.
The family company W&H Dentalwerk in Bürmoos, north of Salzburg, has been placing the highest requirements on the training of its young members of staff for many years now. Instructor Matthias Hufnagl is certain that the future is in state-of-the-art CNC technologies, which require extensive IT skills. The aim of the W&H training programme is to prepare the apprentices for the requirements of today's labour market as well as possible.
Starting an apprenticeship at W&H is like laying the foundations for a solid career. In addition to manual skills, complete machining of components with state-of-the-art CNC machines is also a key focus area of the three-and-a-half-year apprenticeship. As early as in the first year, the apprentices get to produce components which are then employed in production.
Curriculum adapted to reflect evolving technological requirements
In order to do justice to the demand in modern industrial companies for optimally trained skilled workers, W&H sets great store by communicating the latest technological expertise in the field of CNC technology. "Although the mechanical basics have barely changed over the years, we have seen rapid developments in the fields of CNC technology and the tools and materials used", said Matthias Hufnagl. "Manufacturing processes which were still performed on cam-controlled lathes until a few years ago are now completed on state-of-the-art CNC machines.
Of course, these new technological requirements also need to be integrated in our curriculum." In addition to providing state-of-the-art machining systems for training purposes and communicating extensive CNC programming skills, the company from near Salzburg also pays special attention to on-the-job training in production. The apprentices predominantly use machine systems from renowned machine manufacturers well known on the international market.
Focus on well-founded CNC basic training
Every year, W&H offers 10 apprenticeships in the field of metal and machining technology. A positive development: girls are also starting to show more and more interest in the field. W&H currently has four female apprentices training to work in the field of metal and machining technology. "When it comes to applicants, technical and mathematical competence as well as spatial sense are very important factors for us. As we are involved in the production of dental instruments on a micrometre scale (thousandths of a millimetre), a high degree of dexterity, fine motor skills and precision is also required."
The young employees spend their first two years working in the W&H training workshop. In the first year, they focus on manual tasks such as filing, drilling, grinding, threading, sanding and tool theory. "It is important to us that our apprentices start to manufacture parts that we can actually employ in the company from an early stage. The number of purely "practice pieces" is very low nowadays", explained instructor Matthias Hufnagl. In addition to manufacturing an air motor, which already includes the first important steps such as the production of a piston, a piston rod or a fly wheel, the elaboration of a V-block vice for measuring and filing small components is also a good example of the tasks they encounter. This communicates important basics for the handling of the materials which are important at W&H such as stainless steel, bronze, aluminium and even plastics.
Once they have learned the manual basics, they move on to basic CNC training. "Each apprentice is provided with a CNC machine for CNC lathe and milling work. Over the course of a six-month rotation, each apprentice then completes approx. 50 programmes independently", said Matthias Hufnagl. The basic CNC training is also performed in the training workshop. The focus is on the production of assembly tools, which can be used in the W&H service locations.
Project work supports targeted learning
On completion of the second year of training, the young employees then move to the modern W&H production department. The special element here is that they receive support from their "mentors". These experienced employees are on hand with tips and tricks of the trade as well as being responsible for communicating specific knowledge to their charges. In addition to getting to know the machine systems from internationally recognised brands, another focus is project work.
To this end, W&H provides its own project machines which are exclusively used to produce prototypes and pilot runs. "The learning effect for our apprentices is particularly high during the project work. It places particularly high demands on independent thinking and action as well as teamwork", explained Matthias Hufnagl. In order to become familiar with as many machine systems as possible, the apprentices are assigned a new mentor and a new machine every six months in rotation. "This helps us to ensure that they benefit from as wide a range of machine systems as possible and are thus best equipped for the wide range of requirements existing on the labour market", said Matthias Hufnagl.
Awards are proof of extraordinary training level
The numerous national and state awards are particular proof of the extraordinary high level of training we offer our apprentices in the field of metal and machining technology. After W&H apprentices managed to win 2nd and 3rd place in the "CNC lathe work" category at the Austrian national championships last year, we managed to scoop all three podium positions at this year's state championships.
The high number of distinctions in the final apprenticeship exams is also considerable proof of the company's high standard of training for Matthias Hufnagl, who has been a member of the examination board at the WIFI in Salzburg himself for around 10 years.
From precision engineering to mechanical and plant engineering, W&H apprentices are in high demand among the renowned industrial companies in our region. "On successful completion of their training, our young specialists often go on to work in general mechanical engineering and toolmaking, in job order production for CNC lathes/mills and in plant engineering", explained the W&H instructor with pride.
Flexibility – the alpha and omega
Due to the rapid technological change, young people working in metal and machining technology nowadays are required to be highly flexible. "The young people need to be open to the latest technologies. They need to adjust to new machine systems quickly and utilize them successfully", said Matthias Hufnagl.
In addition, he emphasized that the programming skills in the field of CNC are becoming ever more important in comparison with mechanical work. This is a distinct change in the relationship here. "Nevertheless, the connection to the materials is still important and should not be neglected in the apprenticeships of the future. The best solution, obviously, would be if the apprentices can combine the mechanical aspects and the IT aspects without any problems – that would truly be the aim of the apprenticeship", concluded Matthias Hufnagl.
comments