Wie aus Ideen Bestseller werden – in Bürmoos in die Produktionshallen geblickt
W&H fertigt Hand- und Winkelstücke sowie Turbinen seit 1890. Konkret wurden von damals bis heute 10.512.183 Millionen dieser Produkte weltweit verkauft. Diese Aha-Zahl ist genauso beachtlich wie die 76 Einzelteile, aus denen ein Winkelstück der Synea Vision-Serie besteht. Oder den 60 km/h, die ein 1:5 Winkelstück schafft. Oder der Vielzahl an Händen, die täglich in manuellen Montagelinien dafür sorgt, dass jedes Zahnrad den richtigen Platz in der Außenhülse findet. Tobias Schwarz (Management Product-Innovation) und Herbert Schörghofer (Leitung Produktion) geben Einblicke in die hochmoderne Produktion und verdeutlichen, warum ‚Made in Austria‘ die beste Entscheidung für beständige Produkte ist.
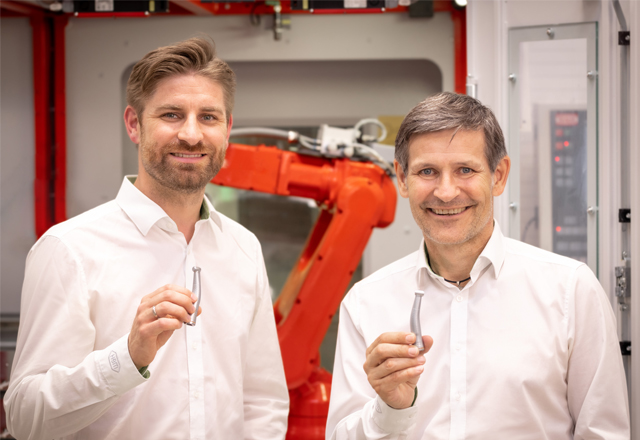
Seit 1890 entwickelt und produziert W&H Turbinen und Winkelstücke. Was zeichnet die Produktion heute aus? Gibt es Schnittmengen zu damals?
Schörghofer: Die Produktion bei W&H ist im Vergleich zu damals hochautomatisiert und es werden nur die modernsten Maschinensysteme verwendet. Früher brauchte man für komplizierte Teile bis zu vier verschiedene Maschinen. Heute werden die komplexesten Teile auf einer Maschine fertiggemacht. Damit können wir qualitativ hochwertig, schnell und gleichzeitig sehr wirtschaftlich produzieren.
Was man durchaus als Schnittmenge zu 1890 bezeichnen kann ist das noch immer gleiche Antriebsprinzip von Turbinen und Winkelstücken und die damit verbundene Ähnlichkeit der Teile. Zwar haben sich die Materialien und die Formen verändert, aber es geht noch immer um Zahnräder, Laufräder, Achsen, Spannzangen, Außenhülsen, Halsstücke oder Köpfe. Auch das Montieren passiert großteils immer noch von Hand.
Wodurch erlangt W&H heute eine so hohe Produktionstiefe?
Schörghofer: Im Grunde ist ein hoher Eigenfertigungsanteil schon immer das Prinzip von W&H. Damit haben wir die Sachen selber in der Hand und wir wissen auch, dass es passt. Zweiter wichtiger Punkt sind unsere hochqualifizierten Mitarbeiter.
Viele Lieferanten kommen unmittelbar aus der Region. Welche Vorteile ergeben sich daraus?
Schörghofer: Der Familie Malata war es schon immer wichtig, Lieferanten aus der näheren Umgebung zu gewinnen, um das regionale Wirtschaftswachstum zu fördern. Dazu streben wir langfristige, partnerschaftliche und vertrauensvolle Beziehungen an. Da lässt es sich auch in schwierigen Zeiten besser reden, kurze Entfernungen lassen schnellere Reaktionen zu und es ist immer ein Vorteil, wenn man sich persönlich kennt.
Was bedeutet ‚Made in Austria‘ für Sie persönlich?
Schörghofer: ‚Made in Austria‘ wird weltweit als Gütesiegel für eine Top-Qualität verstanden. Es gab bei uns sehr lange den Leitsatz „Qualität und Präzision haben einen Namen: W&H“. Für mich bedeutet ‚Made in Austria‘ nichts anderes als das. Klar ist auch, die Kunden erwarten von W&H als österreichische Firma nicht nur Top-Qualität, sondern auch einen top After-Sales-Service sowie freundlich-kompetente Ansprechpartner.
Wie steht es um den Bereich FuE, ist auch dieser in Bürmoos ansässig?
Schwarz: Die Entwicklung neuer Produkte hat bei W&H einen besonders hohen Stellenwert. Unser Ziel ist es, Produkte für unsere Kunden mit neuen Funktionalitäten auszustatten, um den Arbeitsablauf in der Praxis immer wieder zu verbessern. Zu diesem Zweck sind wir besonders im Produktmanagement sehr eng mit unseren Kunden vernetzt, um Bedürfnisse zu identifizieren und durch clevere Lösungen Probleme des zahnärztlichen Alltags zu lösen.
Wesentliche Errungenschaften sind hier zum Beispiel der Einsatz von extrem miniaturisieren LEDs in Turbinen zur optimalen Beleuchtung der Behandlungsstelle. Ebenso spielt die richtige Auswahl der verwendeten Materialien eine große Rolle, um die Beständigkeit unserer Produkte bei der hygienischen Aufbereitung sicherzustellen.
Bitte skizzieren Sie uns den Weg eines Winkelstücks.
Schwarz: Die Reise beginnt damit, dass wir durch genaue Beobachtung der Anwender und proaktive Rückmeldungen konkrete Anforderungen an das Produkt ableiten. Es folgte eine Phase, in der Lösungsideen gesucht, analysiert und in Form von Prototypen realisiert werden. Mit Anwendern wird das Ergebnis oft durchaus kritisch bewertet und dann der optimalste Ansatz zur Finalisierung gebracht. Nun gilt es, die hohen gesetzlichen und regulativen Anforderungen an Medizinprodukte hinsichtlich klinischer Leistungsfähigkeit und Sicherheit sicherzustellen. Das CE-Zeichen auf unseren Produkten ist dafür der sichtbare Beweis.
Aus wie vielen Einzelteilen besteht ein Winkelstück?
Schwarz: Das ist eine sehr gute Frage deren Antwort oft verblüfft. Von außen sehen Winkelstücke aus wie ein Stück Metall. Darin steckten jedoch eine Vielzahl an verschiedensten, perfekt aufeinander abgestimmten Präzisionsteilen. Am Beispiel des roten Winkelstücks WK-99 LT aus der Synea Vision Serie sind es konkret 76.
Haben Sie ein Lieblingsprodukt innerhalb dieses Sortiments?
Schörghofer: Aus dem Winkelstücksortiment würde ich das rote Winkelstück nehmen, also unser WG- oder WK-99. Dieses Winkelstück war und ist das Flaggschiff unter den Winkelstücken. Kräftig, schnell und präzise aber auch elegant und langlebig. In diesem Medizinprodukt sind die typischen W&H-Fähigkeiten aus Fertigung und Entwicklung bestens vereint.
Schwarz: Das rote Winkelstück ist auch mein Favorit. Darin steckt die DNA von W&H – höchste Präzision und Zuverlässigkeit.
Kommentare