Dental instruments - more than just a tool
Silicon oxide – the secret behind surface sealing
The comparison clearly shows that while instruments with a conventional coating (on the left) are already displaying significant signs of wear after two years of practice use, instruments coated with silicon oxide (on the right) exhibit no signs of use at all.
The chrome-plated stainless steel outer parts owe their robust properties to the innovative silicon oxide layer. W&H has already filed a patent application for this coating. Thanks to the unique combination of high-grade base metal and an ultra-thin sealing layer, the W&H instruments are characterized by maximum robustness and value retention. However, not only is the lifetime significantly increased: the aesthetic appearance of the instruments is also maintained for several years - clearly an asset for any modern dental practice.
High-quality, well-serviced handpieces are the calling card of a well-managed dental practice. Their outer appearance, however, quickly loses its shine due to the high loads exerted during the preparation process. W&H can provide perfect surface protection with the help of the latest coating technology. Signs of wear and tear are now a thing of the past. The high-quality instruments fully meet the aesthetic requirements of both patient and dentist.
Nowadays, a well cared for exterior is a matter of course in many areas of life. Our first impression of people is heavily influenced by their outer appearance. We judge them completely subconsciously within a matter of seconds. This first impression is also a key factor in dental treatments: the patient draws conclusions about the quality of the treatment from looking at the dental instruments. To the dismay of dentists, many instruments tend to look worn and unsightly after only a short time due to the high demands placed on them during sterilization and reconditioning. The instruments give an outdated impression despite the fact that they function perfectly.
Innovative surface ensures perfect appearance
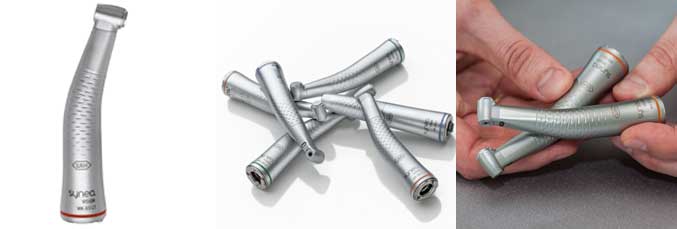
Following the market’s requirement for durable products, W&H developed a unique scratch-resistant surface. The aim of this additional coating is to increase the durability and longevity of the dental handpieces and also to convey a high-end impression. Surgical instruments, along with the Synea Vision range, are provided with this innovative coating. As a result, W&H products offer maximum robustness even under extreme loads.
W&H develops its products exclusively in close collaboration with the user. Information regarding the essential needs of patient and dentist was collected in many discussions with dentists all over the world. Michael Pointner, Strategic Product Manager, says, “We were particularly surprised by the enormous influence that a dental practice’s surroundings have on the patient’s mood. We defined our product requirements based on this knowledge. Our primary aim is to meet the high demand for quality expressed by the dental practices.”
Tested by users
A number of different coatings were investigated for their usability in the W&H research and development department; they were tested in the laboratory and ultimately trialled by dentists in routine daily practice work. Dipl.-Ing. Beate Wagner was in charge of this. The materials scientist says that developing a coating that would satisfy the exacting requirements for instrument surfaces posed a particular challenge.
“During development, the aim was to find a coating that was characterized by excellent durability and high wear resistance. During their lifetime, instruments pass through a huge number of conditioning cycles. It is therefore important that the surface can withstand the extreme loads,” Wagner explains. “Other aspects are the instrument’s grip, the coating’s biological compatibility and the possibility of easy cleaning. We can meet all these criteria perfectly by applying an innovative inorganic coating. The coating is produced using a special process known as plasma-enhanced chemical vapour deposition and offers optimum all-round protection.”
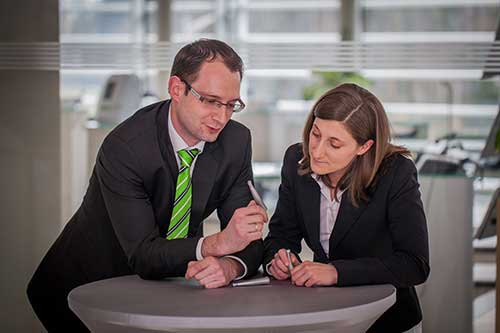
The innovative surface coating is the result of intensive development work. Strategic Product Manager Ing. Michael Pointner and materials scientist Dipl.-Ing. Beate Wagner are convinced that this will address important market requirements.
Initial positive feedback from users confirms the high relevance of the new W&H scratch-resistant surface coating in routine daily practice work. “Compared to our conventional coatings, which after some time exhibit signs of use on the instruments, the new process offers lifetime protection. Even after several years of daily use, there are no significant signs of surface damage on the surface of the instruments,” according to Michael Pointner.
The new surface coating was put to the test with the help of the dentists who took part in the trial. The W&H instruments were in trial use for two years. “After the test phase was complete, the feedback for W&H was crystal clear: the majority of the test users were so enthusiastic about the innovative coating that they requested other instruments in comparable quality.”
comments